Extractive Review: Overview
EnvIRONment and Other Bath Smelting Processes for Treating Organic and Ferrous Wastes
S. Street, G. Brooks, L. Reilly, and H.K. Worner
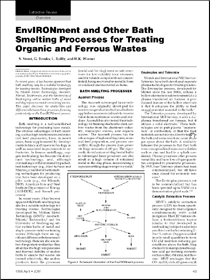 |
CONTENTS |
---|
|
In recent years, it has become apparent that bath smelting may be a suitable technology for treating wastes. Technologies developed by Molten Metal Technology, Ausmelt, Mintek, Techtronics, and the University of Wollongong utilize molten baths of metal and slag to process metal-containing wastes. This paper discusses the similarities and differences between these processes, focusing particularly on the EnvIRONment process.
Bath smelting is a well-established technology for producing base metals. The obvious advantages of bath smelting, such as high reaction rates and minimal feed preparation, have, in recent years, been supplemented by developments in lance and tuyere technology as well as associated improvements in refractories. In ferrous metallurgy, oxygen steelmaking has become the dominant technology, and, although ironmaking is still dominated by packed-bed technology (e.g., blast furnace and Midrex), a number of bath smelting technologies for producing iron have been developed on a pilot scale (e.g., the HIsmelt, DIOS, American Iron and Steel Institute-Department of Energy [AISI-DOE], and Romelt processes).
In recent years, it has become apparent that bath smelting may also be a suitable technology for treating wastes. Technologies developed by Molten Metal Technology (MMT),1 Ausmelt,2 Mintek,3 Techtronics,4 and the University of Wollongong utilize molten baths of metal and slag to process metal-containing wastes. Although there are significant differences between each technology, there are also a number of important similarities: they all utilize the high temperatures and thermal stability of molten baths to ensure that wastes are treated effectively; the molten products from the processes (metal and/or slag) serve as safe reservoirs for low-volatility toxic elements; and the volatile components are concentrated, being recovered in metallic form or oxidized and recovered as fume.
The Ausmelt submerged lance technology was originally developed for nonferrous production but has also been applied on a commercial scale to recover value from nonferrous wastes and residues. Ausmelt has also tested their technology for treating steelworks dust, carbon wastes from the aluminum industry, municipal wastes, and organic wastes.2 The Ausmelt process has the advantages of high smelting rates, minimal feed preparation, and process versatility, though the process does generate large amounts of off-gas. The rigorously stirred nature of slag/metal baths in submerged lance processes can also result in a high volume of entrained metal in the slag phase, necessitating a separate settling stage to improve yield.5
Mintek and International Mill Service-Tetronics have both developed separate plasma technologies for treating wastes. The Enviroplas process, developed by Mintek since the late 1980s, utilizes a hollow electrode in a direct current (d.c.) plasma transferred arc furnace. A proclaimed feature of the hollow electrode is that it enhances the ability to feed unagglomerated material to the bath.6
The Tetronics process, developed by IMS, is also a d.c. plasma transferred arc furnace, but it utilizes a solid electrode.7 These technologies are in part plasma "incineration" or combustion, in that the feed materials are not always directly fed into the bath and some reactions occur in the gas space above the bath. A similarity between the processes is that they both were conceptualized to recover volatiles such as zinc and lead in a splash condenser. Plasma processes offer process versatility and have low off-gas quantities compared to pneumatic processes. By 1995, four Tetronics plants had been commercialized, but all have since closed for economic reasons.8
The Enviroplas process is yet to be commercialized but has been operated up to 3 MW on a demonstration plant scale.3,4,9
Molten Metal Technology's catalytic extraction process (CEP) has been specifically designed to treat organics simultaneously with solid inorganics. The CEP furnace utilizes a bottom-blown tuyere (similar to that developed in steelmaking) to inject wastes into a molten iron bath containing 2-3 wt.% carbon. Oxygen is added in only small quantities to form CO and maintain reducing gas conditions above the bath. Slag chemistry is manipulated to capture acid gas-forming elements such as sulfur, chlorine, and fluorine.1 Molten Metal Technology envisages that the CO- and H2-rich off-gases could be sold as fuel gas.1 Molten Metal Technology is currently in partnership with Hoechst, the Westinghouse/SEG partnership, and Lockheed Martin to build and commission pilot and full-scale plants for treating a wide range of wastes, including chemical, petrochemical, pulp and paper, textiles, and metallurgical.10
To date, one of the most comprehensive projects investigating the application of bath smelting to processing metallurgical wastes has been the American Iron and Steel Institute-Department of Energy Direct Steelmaking Waste Oxide Recycling Program.11 Evaluation trials of this technology began in April 1994 and were deemed sufficiently successful that the trial work was completed only eight months latertwo months ahead of schedule.12 Agglomerated feed was charged into the top of the smelting vessel together with coal or coke breeze; waste fines were also pneumatically injected into the slag layer. The smelting vessel was operated under pressure; top-blown oxygen was used for post-combustion, and bottom-injected nitrogen was used for bath stirring. A hot cyclone (900°C) was used for the first stage of off gas cleaning, removing the majority of solid particles. Products from the bath smelting of the steelworks wastes included hot carbon saturated iron, slag that passed the toxicity characteristic leaching procedure, and zinc-rich sludge.
Although the American Iron and Steel Institute-Department of Energy program is being heralded as leaving "no substantial questions unanswered on this technology for recycling steel plant waste oxides,"12 the existing economic climate has dissuaded the construction of any plants. A demonstration plant was to be built at Stelco's Lake Erie site, but the project was halted because of financing problems;13 currently, process viability is seen as being subject to the costs of landfill.14
Under development by Illawarra Technology Corporation (ITC), the business arm of the University of Wollongong, the EnvIRONment process is designed to treat ferrous wastes simultaneously with organic wastes.15-17 The major products of the process are foundry grade iron and disposable slag. In the electric-arc-furnace-based process, a molten slag layer is maintained above an iron bath, which serves as both a medium for reducing the metal oxides in the pelletized feed and breaking down organic molecules in the composite pellets into simple molecules. Volatile metals such as zinc, cadmium, and lead are recovered in the bag house. Off-gases are rich in carbon monoxide and hydrogen and have significant fuel value.
The EnvIRONment process was initially tested using steelworks dust and sewage sludge, but this work has been extended to consider a wide range of organic, non-volatile carbon and ferrous waste streams. Research has identified that the reaction mechanisms are different than those found in bath smelting processes that do not use a composite feed material. Evidence indicates that smelting occurs with a significant reduction within the pellet; as a result, limited slag foaming occurs. Reaction rates are relatively fast, with much of the iron oxide being reduced and carburized before pellet dissolution is complete.
Shown schematically in Figure 1, the EnvIRONment process was initially developed in 1990 on a bench scale. Since 1993, however, work has proceeded using a 100 kg d.c. electric arc furnace. Electric furnace technology was chosen for the process ahead of a pneumatic system because it was easier to apply at a small scale, it allowed greater control of the metallurgy by allowing the slag layer to be readily heated to above 1,500°C, and it produced a much lower volume of off-gases.
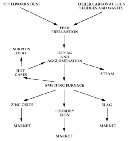 |
Figure 1. Schematic illustration of the EnvIRONment process. |
The process was initially tested using steelworks dust obtained from the BHP Port Kembla steelworks and sewage sludge from the state water board. The steelworks dust consisted of combined belt-press sludge from the blast furnaces and basic oxygen steelmaking (BOS) fume collection waste; it contained between 1-4% zinc and small amounts of lead. The ratio of dust to sludge was typically 6 to 1 (dry weight basis). Kish graphite and other low volatile carbon was added to the mix to provide sufficient carbon for reduction and carburization. Lime was also added in the form of BOS slag to produce the appropriate slag chemistryone of the repercussions of using this dilute form of lime in the trials was excessive slag production. The feed was first mixed and than extruded into 20 mm X 20 mm cylinders (pellets) and dried. Using a conveyer system, the pellets were fed continuously into a 100 kg slag- and metal-containing d.c. electric arc furnace. The temperature was held above 1,500°C. Slag and metal were periodically tapped from the furnace into ingot molds. Initially, off-gases were post-combusted outside of the furnace; they cooled rapidly and traveled through the baghouse, wet scrubber, and a carbon filter before being released into the atmosphere.
This processing route produced foundry grade iron (3.5-4.6% C, 0.1-0.4% P, 0.1-0.5% Mn, 0.05-1.0% Si, 0.01-0.1% S, 0.01-0.03% Ni, 0.01-0.03% Cr, and 0.005-0.01% Ti), benign slag (0.4-3.0% FeO, 26-33% SiO2, 7-15% Al2O3, 37-45% CaO, 0.5-1.5% MnO, 7-15% MgO, 0.01-0.1% P, 0.05-0.2% Na2O, 0.1-1.0% S, and 0.1-0.5% F), and harmless off-gas. The iron produced is similar in quality to that produced from a blast furnace and is most definitely superior to the direct-reduced iron and scrap available on the ferrous market. The relatively high phosphorus values were due to the high phosphate values in the sewage sludge and the highly reducing nature of the furnace. Standard leachability tests carried out on the slags consistently demonstrated that the slags produced are readily disposable.
At the current scale of testing, several major technical issues have been addressed, including establishment of the most effective combination of low- and high-volatility carbon in the pellet feed, determination of the best mixtures for producing pellets with appropriate mechanical properties, determination of the most appropriate slag chemistry, and establishment of the optimum furnace processing conditions. A wide range of organic, non-volatile carbon, and ferrous wastes have been tested. Significant attention has also been paid to the method of agglomeration; extrusion, centrifuge, and roll briquetting techniques have been tested.
The EnvIRONment process is, in a sense, antithetical to combustion as feed materials in combustion processes are completely oxidized; in the EnvIRONment process, the feed materials are reduced from their oxidized state back to their basic elements, as per
Fe2O3 + 3C (g) = 2Fe + 3CO (g) |
(1) |
Cr2O3 + 3C (g) = 2Cr + 3CO (g) |
(2) |
CxHyO = xC + y/2H2 (g) + CO (g) |
(3) |
C + CO2(g) = 2CO (g) |
(4) |
These highly reducing conditions prevent the reforming of compounds in the gas space above the molten bath, which is always a major concern in treating toxic organic compounds via conventional combustion. The carbon monoxide atmosphere in the furnace is maintained by establishing the appropriate stoichiometry and keeping the molten iron bath in the furnace virtually saturated with carbon (typically 4.5 wt.% carbon in the iron). The highly volatile carbon of the organics must be supplemented by less volatile (low reactivity) carbon to contribute to the reduction reactions and to carburize the iron bath. There are several appropriate "wastes" that serve as sources of low volatility carbon, including kish graphite from the iron and steel industry, electrode carbon, and coke fines.
The molten slag layer produced above the iron bath serves as both a medium for reducing the metal oxides in the pelletized feed to metal and for breaking down the organic molecules in the composite pellets to simple molecules such as carbon monoxide, carbon dioxide, hydrogen, and water vapor. The thermal stability of the iron and slag bath ensures that all the waste materials in the pellets are treated and that there is no easy route for toxic compounds to escape, as is sometimes a problem with incineration processes. The generation of gas from the pellets during smelting creates localized stirring in the slag layer and assists in the dissolution of the pellets due to increased heat transfer.
Fluxing materials, such as lime, may also be required as a feed to the process (depending on the chemical make-up of the various waste streams) to provide the appropriate slag chemistry for producing a salable iron product. During smelting, the slag layer is slightly foamedmore specifically, it is agitated in close proximity to the reacting composite pellets. Like many aspects of the process, the chemistry and physical properties of the slag are well understood and easily controlled, as they have been extensively studied by researchers in the iron and steel industry.
The metal and slag products from the process serve as safe reservoirs for low-volatility toxic elements. Iron and transition metals (e.g., Mn, Ni, Cr, and V) are captured in the metal phase. High-value iron products, such as chromium-iron, can be made by combining feed materials in the appropriate way. The slag produced from the process is comparable to that produced from steelmaking, albeit with far less iron content; potentially it could be used for landfill, ballast, aggregate in asphaltic concrete, and as a soil conditioner.18 Small quantities of elements such as S, Na, K, and Ti can be safely encapsulated in the slag.
Volatile metals (e.g., Zn, Cd, and Pb) are recovered in the baghouse. The amount of fume recovered represents a small fraction of the input fume feed; typically, less than two percent of input wastes would be recovered as dust, although the exact figure will greatly depend on the amount of volatile metals present in the feed streams. Any value that the collected fume may have will largely depend on the concentration of zinc in the fume. A high-zinc-content fume (>30 wt.%) with minimal contamination from iron could be sold as a feedstock to the zinc industry. Low iron content can be achieved by producing pellets that are mechanically stable, which prevents dust carry-over from the electric arc furnace to the baghouse.
The off-gases from the process are rich in carbon monoxide and hydrogen; therefore, they have significant fuel value. The sensible heat and combustion heat recovered from the off-gases would, in most cases, exceed the energy requirements for drying and pre-heating the feed. In general, the gases are not used for pre-reducing the feed, as this would require direct contact between the gases and the feed at temperatures lower than those maintained in the furnace; this would risk the generation of toxic gas compounds. The possibility of dioxin formation during the combustion of the off-gases can be minimized by using excess oxygen, mixing the gases effectively, and rapidly cooling the gases through the 200-400°C range.19 Because the rationale of the EnvIRONment process is not to utilize pre-heating or pre-reduction, the process infrastructure is comparatively simple, with waste treatment being confined to a single-vessel reactor.
The fundamental studies on the EnvIRONment process at the University of Wollongong have concentrated on characterizing the iron-bearing dusts, consolidating and characterizing the composite pellets, and studying the reaction kinetics and mechanisms of the smelting process.20-22 Theoretical modeling has also been used to investigate the thermodynamic and heat transfer fundamentals of the process.
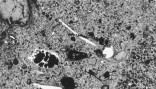 |
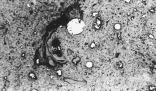 |
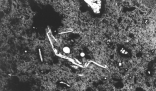 |
Figure 2. Typical microstructures of the composite pellets.
|
The composite pellets were found to have a drop strength of 33 DFM (drop from a meter), with a range of 17-58 DFM. The measured drop strength exceeded published values for other pelletized ferrous systems.23-25 The dry compressive strength was measured to be 156 N; although this value is less than that for many indurated ore pellets, it is still relatively high for a cold-bonded material. Compression testing of the composite pellets showed them to be very resilientafter reaching the peak compressive load, the pellets deformed plastically rather than catastrophically via brittle fracture mechanisms. Abrasion of the pellets in the 100 kg d.c. arc furnace feed system (vibratory unit) was very minor. The thermal shock resistance of the pellets is high, as the pellets did not spall or catastrophically fail on being charged onto a slag at 1,500°C. The pellets have an apparent porosity of 52 percent with a bulk density of 1.38 g/cm3the porosity being much higher than other pelletized ferrous systems. Optical microscopy also revealed that the porosity of the composite pellets was not uniform, with tortuosity and pore structure varying considerably. Indeed, the microstructural and mineralogical characteristics of the composite pellets are complex and diverse, exhibiting localized non-homogeneity (Figure 2).
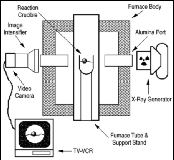 |
Figure 3. Schematic diagram of x-ray apparatus for studying smelting-reduction reactions.
|
Research into bath smelting and the treatment of iron and steelmaking wastes shows that binders are critical in pyrometallurgical processing.6,11,26-28 The superior strength properties of the composite pellets are thought to result from the excellent binding properties of the bio-solids component, with the sewage sludge being a non-rigid binder.
Studies into process reaction mechanisms show that the EnvIRONment process is fundamentally different than other bath smelting methods, such as the DIOS and American Iron and Steel Institute-Department of Energy processes. In these latter processes, the critical process reactions are the reduction of dissolved ore from slag by char and Fe-C droplets, carburization, and slag foaming.29 However, the evidence for smelting the composite materials suggests that most of the reduction occurs within the agglomerated feed rather than the slag phase.
Laboratory smelting experiments observed using x-ray fluoroscopy (Figure 3) revealed that the composite pellets float on the slag layer, that gas evolution results in pellet motion, and that slag foaming is relatively limited. After single pellet smelting trials, the extent of foaming could be physically measured by analyzing slag erosion marks on the reaction crucible. Using the equation
 |
(5) |
(where S is the foaming index, H is the foam height, and Vg is the superficial gas velocity)30 it is possible to calculate the potential slag height generated during smelting. For a typical bath smelting slag with a low FeO content, the foaming index has a value of approximately 2.31 Calculations based on the iron oxide content of the pellet predicted that the slag should foam to a height of 3.6 cm in the reaction crucible if all of the FeO reduction occurred in the slag. Measurements from the crucible indicated the foam height only reached an average of 0.5 cm (Figure 4). This indicates that not all reduction occurs in the slag phase; back calculation indicates that for the experiments, only approximately ten percent of the reduction occurred here.
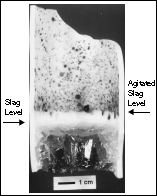 |
Figure 4. Reaction crucible from smelting trials showing slag erosion levels.
|
Experimental evidence from the DIOS and American Iron and Steel Institute-Department of Energy research programs demonstrate that the contribution of the reaction interfaces to overall reduction varies with the size of the smelting vessel.32,33 By extrapolating the pilot-plant data, it is possible to predict for the EnvIRONment process the contribution from the metal-slag interface. Assuming the reduction mechanisms are the same as those operating in the DIOS and American Iron and Steel Institute-Department of Energy bath smelting processes, then the 100 kg d.c. arc furnace reduction at the metal-slag interface accounts for 80-100% of the total reduction. At such high contributions, slag foaming would be considerable as the majority of reaction gases would evolve at the bottom of the slag layer. Pilot-plant smelting trials clearly show that this not the case, thereby supporting the notion that reduction does not primarily occur in the slag phase.
Further experimental evidence that most reduction occurs within the agglomerated feed was found when smelting trials were examined using x-ray radiography. Images taken during smelting show the existence of dense spheres within the composite pellet well before the completion of reduction. Partially smelted pellets have been recovered, typically after 45 seconds, from laboratory trials. Microscopy indicates that ablation of the composite pellets occurs partially through the dissolution of FeO but primarily via the loss of metallic iron, with iron droplets coalescing on the outside of the pellets before separating and descending through the slag layer. Figure 5 shows a partially smelted sample that has been selectively etched to show that the iron present in the pellet is significantly carburized during smelting (i.e., much of the iron is carburized within the pellet before it is completely dissolved).
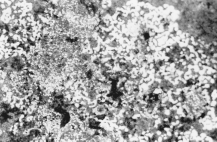 |
Figure 5. Microstructure of partially smelted sample selectively etched to highlight carburized iron.
|
Typically, smelting times are in the range of 60-180 seconds, which is faster than comparative treatment technologies. Enhanced reaction rates can be explained by the extent of internal direct reduction within the pellet during smelting. Studies elsewhere show that for gaseous reduction systems, the rate of reaction in a powdered mixture of oxide and carbon are an order of magnitude greater than for separated material.34 Gaseous reduction experiments used to investigate reduction mechanisms in the composite pellets are described elsewhere,22 but have confirmed that reduction for slow heating rates is substantially sequential; reaction overlap was evident in the smelting trials because of the faster heating rates, as the reaction is topo-chemical and heat-transfer dependent.
Heat-transfer control is suggested by closer scrutiny of the pellets' smelting behavior. Microscopy of partially smelted samples revealed a diffuse reaction front, indicating that a temperature gradient exists within the pellet during smelting. The ingress of the reaction front was not uniform but clearly exhibited a weighting toward the slag-pellet interface, particularly during the early stages of smelting. Forcibly submerging pellets into the slag increased smelting rates; deeper submersion into the iron bath resulted in rapid and vigorous reaction.
In order to gain an understanding of the heat-transfer principles operating in the EnvIRONment process, a series of models was developed. Although the process operates as a single vessel reactor, it was necessary to model the process in two distinct stagesa short intermediate stage falling-gas region (where heating occurs as the pellet falls through the gas space in the bath smelter) and an in-slag smelting region (where heating is accompanied by dissolution in the slag phase).
In the falling-gas region, the pellet was reasoned to be in a forced convection situation with heat transfer being controlled by internal resistance; the effective heat-transfer coefficient being calculated as 365 W/m2 · K. In the falling- gas region stage, the pellet's center temperature barely rises (~10°C); the predicted temperature profile generated is exponential, meaning that a significant volume of the pellet undergoes considerable heating.
Developing a heat-transfer model for the in-slag smelting region proved more difficult. The complexity of not only the smelting process but the material itself meant that many simplifying assumptions were necessary to develop at least a qualitative understanding of heat transfer. It is reasoned that, due to internal resistance control, no immersion crust would form on the pellet when entering the slag and that the pellet would quickly loose its momentum from falling, with the pellet remaining fully immersed and motionless in the slag phase. Heat transfer between the slag and the pellet, being in a natural convection condition, was calculated to be 1,400 W/m2 · K.
Smelting was treated as a two-phase moving boundary problem and solved using a computer program. Heat transfer was described using Fouriers law. Temperature in the pellet is expressed as
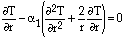 |
for 0 < r < R |
(6) |
|
 |
for r = 0 |
(7) |
|
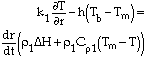 |
for r = R |
(8) |
By developing finite-difference equations by a Taylor's expansion of Equations 6 and 8
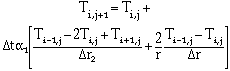 |
(9) |
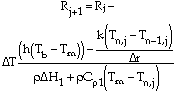 |
(10) |
where solution stability is found when
 |
(11) |
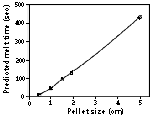 |
Figure 6. Influence of pellet size on melting time predicted by a heat-transfer model.
|
The results for the model are shown in Figure 6. For a 20 mm particle, the predicted melt time is 136 seconds; increasing particle size increases the time required for melting. Of the assumptions necessary for model development, the most necessary (in terms of simplicity) was that in the in-slag smelting region, the pellet was fully submerged and in full contact with the slag. In reality, experimental observations show that the pellet is not fully submerged and is not in continuos contact with the slag. The composite pellet, being much lighter in density than the slag, floats, thereby limiting slag contact to a small region. Thus, modeling heat transfer has to account for convection and radiation from the gas space above the slag bath (to which the greater part of the pellet's surface area is exposed) and convection from the slag phase. Clearly, the pellet will be exposed to considerably different levels of heat transfer, calculated to be approximately 1:4; this suggests that uniform dissolution is reliant on pellet motion. Pellet motion, in the form of tumbling, has been sufficient in both pilot-plant and laboratory trials that smelting proceeds in a topochemical manner.
Since 1994, Illawarra Technology Corporation has been moving toward commercialization by identifying niche markets, developing process flowsheets, developing economic models, and attempting to form strategic alliances between waste producers and potential process operators. The process has particular applicability to integrated steelworks, in that the process can treat the range of iron-bearing dusts, scale, grinding swarfs, refractory wastes, carbon fines, and various sludges. An audit of one large steelmaking facility identified more than 40 waste streams that could be treated by the process.
Based on in-house and independent analyses, it should be profitable to run an EnvIRONment operation. For example, a plant in eastern Australia treating 100,000 wet tonnes per year of wet organic and iron-bearing wastes should be able to achieve an after-tax internal rate of return between 18-37% annually (based on a $17 million plant producing 20,000 tonnes of iron per year from a seven tonne furnace). The exact return would be sensitive to power prices and the operator's ability to supplement commonly available wastes with high-value waste streams from outside the immediate market.
The authors are grateful to the management of ITC Ltd. for permission to publish this paper. On behalf of ITC Ltd., appreciation is also expressed to Pacific Power and the (Sydney) Water Board for financial support and to BHP, Comsteel, Bradken, and the CSIRO Division of Coal and Energy Technology for physical assistance in a number of ways. The authors also wish to acknowledge the contributions of R. Eshman, D. Harris, B. Robinson, P. Monroe, and Dr. Subagyo to research in the discussed areas that are currently being carried out at the University of Wollongong. The authors also acknowledge the Center for Iron and Steel Research at Carnegie Mellon University, in particular B. Ozturk, R. Fruehan, and A. Cramb for the use of the x-ray facilities.
1. C.A. Chanenchuck and D.L. Hoey, Proceedings of Pyrometallurgy for Complex Materials and Wastes (Warrendale, PA: TMS, 1994), p. 163.
2. J.M. Floyd, Proceedings of The Howard Worner International Symposium on Injection in Pyrometallurgy (Warrendale, PA: TMS, 1996), p. 417.
3. N.A. Barcza et al., Proceedings of Extraction and Processing for the Treatment and Minimization of Wastes (Warrendale, PA: TMS, 1994), p. 941.
4. C.D. Chapman et al., Proc. of Pyrometallurgy 95 (Inst. Min. Met. 1995), p. 243.
5. R.L. Player, C.R. Fountain, and J.M.I. Tupperainen, Mervyn Willis Symposium and Smelting and Refining Course (Melbourne, Australia: University of Melbourne, 1992), p. 20.1.
6. N.A. Barcza et al., Proceedings of Extraction and Processing for the Treatment and Minimization of Wastes (Warrendale, PA: TMS, 1994), p. 941.
7. D.T. Bunney, M.S. Mazanek, and J.K. Pargeter, Residues and Effluents-Processing and Environmental Considerations (Warrendale, PA: TMS, 1992), p. 213.
8. C.D. Chapman et al., Pyrometallurgy '95 (Inst. Min. Met., 1995), p. 243.
9. Anon., http://www.mintek.ac.za/Pyromet/EnviroS.html.
10. 1995 Report to Shareholders (Waltham, MA: Molten Metal Technology, 1995).
11. B. Sarma, K.B. Downing, and E. Aukrust, Iron and Steelmaker, 23 (12) (1996), p. 45.
12. Anon., JOM, 47 (4) (1995), p. 3.
13. G.J. McManus, Iron and Steel Engineer, 73 (1) (1996), p. 50.
14. L. Kavanagh, Iron and Steelmaker, 24 (5) (1997), p. 1.
15. G.A. Brooks and H.K. Worner, Proc. of Pyrometallurgy 95 (Ints. Min. Met., 1995), p. 235.
16. H.K. Worner, Australian patent 638559 (1993).
17. H.K. Worner, U.S. patent 5,364,441 (1994).
18. S.D. Prosser, International Conference on Pyrometallurgy for Complex Materials and Wastes (Warrendale, PA: TMS, 1994), p. 49.
19. J.F. Unsworth et al., Trans. IChemE, 73B (1995), p. 123.
20. B.A. Robinson, B.E. thesis, University of Wollongong (1994).
21. P.J.Monroe, B.E. thesis, University of Wollongong (1995).
22. S.J. Street, G.A. Brooks, and H.K. Worner, CIM Quarterly, in print.
23. K.V.S. Sastry, A. Negm, and T. Kater, Agglomeration '854th International Symposium on Agglomeration (Warrendale, PA: AIME, 1985), p. 41.
24. D.R. Fosnacht, Agglomeration '854th International Symposium on Agglomeration, AIME, 1985, p 387.
25. H.J.Roorda, et al., 3rd International Symposium on Agglomeration, ISS, 1981, p B152.
26. Y. Kanda, et al., Stahl and Eisen, 24 (1976), p. 398.
27. Anon., "The Inmetco Direct ReductionThe Concept for Steel Mill Waste Recycling," company brochures.
28. C. Takano, Scottsdale, private communication (October 1996).
29. G.R. Belton and R.J. Fruehan, Ethem T.Turkdogan Symposium, Fundamentals and Analysis of New and Emerging Steelmaking Technologies (Warrendale, PA: ISS, 1994), p. 3.
30. K. Ito and R.J. Fruehan, Met.Trans B, 20B (1989), p. 509.
31. R. Jiang and R.J. Fruehan, Met.Trans B, 22B (1991), p. 481.
32. H. Katayama, et al., ISIJ Int., 32 (1) (1992), p. 95.
33. R.J. Fruehan, Proc. of the Savard/Lee International Symposium on Bath Smelting (Warrendale, PA: TMS, 1992), p. 233.
34. M.C. Abraham and A. Ghosh, Ironmaking and Steelmaking, 6 (1) (1979), p. 14.
ABOUT THE AUTHORS
S. Street earned his M.E. in materials engineering at the University of Wollongong in 1994. He is currently a postgraduate student at the University of Wollongong. Mr. Street is also a member of TMS.
G. Brooks earned his Ph.D. in extractive metallurgy at the University of Melbourne in 1994. He is currently a senior lecturer in the Department of Materials Engineering at the University of Wollongong. Dr. Brooks is also a member of TMS.
L. Reilly earned his assoc. diploma in metallurgy at Wollongong TAFE in 1981. He is currently a technologist at South Coast Equipment Pty. Ltd.
H.K. Worner earned his D.Sc. in metallurgy at the University of Melbourne in 1942. He is currently an honorary professor in the Department of Materials Engineering at the University of Wollongong.
For more information, contact G. Brooks, University of Wollongong, Northfields Avenue, Wollongong, NSW 2522, Australia; telephone (011) 61 2 42214580; fax (011) 61 2 42213112; e-mail geoff_brooks@uow.edu.au.
Copyright held by The Minerals, Metals & Materials Society, 1998
Direct questions about this or any other JOM page to jom@tms.org.