TMS2021 Virtual is an ideal place for graduate students to create the professional networks essential to building a successful career. We encourage you to participate in all of the meeting’s student activities—which are designed for both graduate and undergraduate students—but we also encourage you to look to the next phase of your career by attending some of our young professional activities.
Student Events (for Graduates and Undergraduates)
It’s Not All Zoom & Gloom Student Trivia Contest
Date: Monday, March 15
Time: 2:00 p.m. to 3:00 p.m. EDT
Mark your calendars and plan to join us for this fun student trivia competition. Like the Materials Bowl typically held at the TMS Annual Meeting, this event tests students knowledge of all things related to materials and TMS. Unlike the annual Materials Bowl, this event is open to all students participating in TMS2021. No advance sign-up is required, and you don't need a team to compete. Just try to correctly answer as many of the multiple-choice questions as you can. The top three scores will receive prizes. See you there!
Student Poster Contest
Date: Monday, March 15
Browse your fellow students' work and submit questions during the Monday evening poster contest session. Students who submitted posters for this event will receive additional details from the TMS Programming Team on how to upload and present their work. (Please note that the deadline to submit posters for this session has already passed.)
Student Career Forum
Date: Tuesday, March 16
Time: 2:00 p.m. to 4:00 p.m. EDT
Join us to hear from early-career professionals, as they offer advice and share stories of how they arrived at their current positions. Then find answers to your questions during the live Q&A portion of the session.
Preparing a Winning Resume Package
Date: Wednesday, March 17
Time: 2:00 p.m. to 4:00 p.m. EDT
At this popular annual meeting session, instructors with backgrounds at national laboratories, universities, and industry share their experiences in obtaining and/or recruiting entry-level positions (postdocs, tenure-track faculty positions, etc.) View their presentations and then join in a live Q&A session. No pre-registration is required; just mark your calendars and plan to join us.
Young Professional Activities
View these presentations by early-career professionals delivered at TMS2021 Virtual.
Young Innovator in the Materials Science of Additive Manufacturing Award Lecture
Speaker: Michael Kirka, Oak Ridge National Laboratory
Lecture Title: "Additive Manufacturing of High-Temperature Metals: Present and Future Opportunities"
Date: Tuesday, March 16
Time: 11:00 a.m. EDT
About the Presentation
Technical advancements of the prior century in the manufacture and performance of high-temperature metals have been driven by scientific progress in the areas of casting, powder processing, and alloy design. The emergence and maturation of additive manufacturing technologies has opened a plethora of new processing routes for high-temperature materials and has begun to enable previously unlockable materials innovations and design opportunities. Additive manufacturing technologies such as electron beam powder bed fusion can be considered to reside at the intersection of the traditional fields of welding, powder metallurgy, and casting. Prior knowledge established from these parent fields is instrumental in the development of additive processing; however, additive is at the same time distinctly different due to the complex nature of the thermomechanical process history. Recent efforts in electron beam processing have enabled successful printing of difficult-to-process systems such as nickel-based superalloys and has opened new opportunities for exploration of refractory systems. Looking forward, additive will make possible the fabrication of components with engineered hierarchical microstructures tailored for in-service optimized performance.
About the Speaker
Michael Kirka is the Group Leader of the Deposition Science and Technology Group at Oak Ridge National Laboratory (ORNL). His current research focuses on developing and understanding the limitations in the processing science for high-temperature materials such as nickel-base (Ni-base) superalloys and refractory metals for additive manufacturing processes through understanding their microstructural evolution and resultant process-structure-property relationships. Additionally, Kirka’s work has focused on understanding the long-term mechanical behavior and degradation mechanisms in additive manufacturing materials similar to those observed during service. He joined ORNL in 2014 as a post-doctoral fellow. Kirka earned his B.S. in materials science in 2007 from The University of Michigan, and M.S. and Ph.D. degrees from The Georgia Institute of Technology in mechanical engineering in 2010 and 2014.
Young Professional Tutorial Lecture
Date: Tuesday, March 16
Time: Noon to 1:05 p.m. EDT
Speaker: Wei Xiong, University of Pittsburgh
Lecture Title: "Integrated Computational Materials Design for Alloy Additive Manufacturing"
About the Presentation
Additive manufacturing, as a versatile technique, can produce complex shape components directly for engineering applications. However, it is challenging to perform a comprehensive design for additive manufacturing processes due to its unique microstructure attributes generated by the complex melting/sintering process. The Integrated Computational Materials Design method can be applied to accelerate the new alloy development and processing optimization in additive manufacturing. The method integrates multiscale microstructure engineering approaches, and especially uses the CALPHAD-based ICME approach as a guide tool, to reveal the process-structure-property relationships. Through the development of the CALPHAD-based ICME methods in the Physical Metallurgy and Materials Design Laboratory at the University of Pittsburgh, we are designing different types of high-performance alloys for additive manufacturing and further improving the post-processing of as-built components, which are manufactured by powder-bed fusion and directed energy deposition. In turn, additive manufacturing has also been used as a tool for rapid prototyping to assist in new alloy discovery.
This presentation will be of interest to researchers, engineers, and students who are interested in phase transformations, new alloy development, additive manufacturing, and ICME.
Wei Xiong is the director of the Physical Metallurgy and Materials Design Laboratory at the University of Pittsburgh. He is an assistant professor in the materials science program since September 2016. Xiong got his Ph.D. degree (focus: computational thermodynamics and physical metallurgy) from KTH Royal Institute of Technology and Doctor of Engineering degree (focus: powder metallurgy) from Central South University. In 2012, he moved from Sweden to the USA after his Ph.D. research program. He stayed one year at the University of Wisconsin – Madison before joining Northwestern University as a research associate for alloy development from 2013 to 2016. Using CALPHAD-based ICME tools and advanced manufacturing techniques, he works in materials design based on process-structure-property relationships. Xiong serves on the TMS Alloy Phases Committee (vice-chair), TMS High-Temperature Alloys Committee, TMS Additive Manufacturing Committee, and ASM International Alloy Phase Diagrams Committee. He has received several academic awards, which include: Best Paper Awards of the CALPHAD journal in 2012 and 2013, and the TMS Functional Materials Division Young Leader Professional Development Award 2015. Xiong serves as an associate editor of the journal Science and Technology of Advanced Materials, and an editorial advisory board member of the journal Materials Characterization.
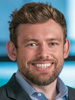
Speaker: James Pikul, University of Pennsylvania
Lecture Title: "Electrochemical Healing of Metals: A New Way to Repair Additive and Cellular Metals at Room Temperature"
About the Presentation
Structural materials in biology can heal fractures at room temperature, whereas metals require elevated temperatures and large energy inputs. As a consequence, modern engineering design follows an approach where a part is optimized to withstand all future loading cases in the part’s projected lifetime. This approach has been highly effective, but results in concepts like safety factors, which increase the weight and volume of the part beyond what's necessary in normal loading conditions. Biology presents compelling alternatives, such as in bone, where ‘parts’ are efficiently produced to withstand most loading cases and, when an extreme case is encountered, the bone can be repaired without being replaced. Manmade structural materials that could heal like bone would have several advantages. A major challenge, however, has been realizing structural metals that can be effectively healed without an expert (in the case of welding, which is prohibitive in complex additive parts) and without high temperatures which consume lots of energy and degrade nearby materials. Recently, we have demonstrated a new rapid, effective, low-energy, and room-temperature approach for healing cellular metals using electrochemistry and polymer-coated cellular metals, which mimic the transport-mediated healing of bone.
In this presentation, I will discuss the advantages of electrochemical healing of metals, new design strategies that emerge through the combined optimization of mechanics and electrochemical transport, and how this approach enables the repair of complex metal parts realized from 3-D printing whose internal geometry prevents repair using current technologies. The combination of electrochemistry, mechanics, transport limited processes, and 3-D structured metals will interest TMS members across diverse areas, such as additive technologies, materials processing, mechanics, corrosion, light metals, and materials design.
About the Speaker