Division Lectures
Structural Materials Division/Functional Materials Division Lecture
Speaker: Rajiv Mishra, University of North Texas
Lecture Title: "Pushing Structural Performance of Materials by Combining Alloy Design with Disruptive Manufacturing Technologies"
Date: Monday, March 15
Time: Noon EDT
About the Presentation
The TMS Structural Materials Division is home to professionals who work on advanced materials for structural applications. Ashby’s framework for materials selection neatly catalogues design approaches under elastic-limiting, strength-limiting, fatigue-limiting, toughness-limiting and creep limiting. Over the years, I had opportunities to work on microstructural tailoring of advanced alloys to maximize strength-ductility combination, to enable exceptional creep resistance, to enhance fatigue endurance limit, and to achieve exceptional high strain rate superplasticity. These studies have included severe plastic deformation to produce nanocrystalline and ultrafine grained alloys. Selective examples will be used to highlight microstructural approaches to influence strength-ductility (including specific strength of ~450 MPa m3/mg), creep resistance and fatigue resistance. The best performance is possible by combining alloy design with disruptive materials processing technologies. This synergistic approach is further enhanced by incorporating multiple deformation mechanisms, such as transformation induced plasticity (TRIP) and twinning induced plasticity (TWIP), through alloy design. Controlling the microstructure and stacking fault energy in high entropy alloys enables progression of TRIP and TWIP mechanisms to delay the onset of failure processes and retard crack growth, pushing the fatigue limit.
About the Speaker
Rajiv S. Mishra (Ph.D. in Metallurgy from University of Sheffield) is a university distinguished research professor at the University of North Texas (UNT). He serves as the director of the Advanced Materials and Manufacturing Processes Institute (AMMPI) at UNT. He is also the director of the National Science Foundation Industry-University Cooperative Research Center for Friction Stir Processing. He is a past-chair of the Structural Materials Division of TMS and served on the TMS Board of Directors (2013 to 2016). He has authored/co-authored >375 papers in peer-reviewed journals and proceedings and is principal inventor of four U.S. patents. His current publication-based h-index is 63 and his papers have been cited more than 21,000 times. He has co-authored two books: Friction Stir Welding and Processing, and Metallurgy and Design of Alloys with Hierarchical Microstructures. He has co-edited fifteen TMS conference proceedings. He is an Associate Editor of Journal of Materials Processing Technology and serves on the editorial boards of Materials Science and Engineering-A, Science and Technology of Welding and Joining, and Materials Research Letters. He is the founding editor of a short book series on Friction Stir Welding and Processing published by Elsevier and has co-authored seven short books in this series.
Extraction & Processing Division/Materials Processing & Manufacturing Division Lecture
Speaker: Richard Russell, NASA
Lecture Title: "Qualification and Certification Strategies for Additive Manufactured Parts for Manned Spaceflight"
Date: Tuesday, March 16
Time: Noon EDT
About the Presentation
The implementation of additive manufacturing techniques to produce critical spaceflight systems is well underway. These technologies will be a key contributor to developing both launch vehicles and spacecraft that will play a crucial role in delivering the first woman and the next man to the surface of the moon by 2024. To assist in the assurance of flight readiness, NASA has created comprehensive certification-based standards for mature technologies for both metallic and non-metallic materials. The presentation will outline the principles of these certification and qualification strategies which are heavily rooted in foundational controls. These foundation controls include process qualification, statistical process control, the development of materials property and design values and the development of a qualified part process.
About the Speaker
Richard Russell currently holds the position as the NASA Technical Fellow for Materials, a position he has held since 2016. Russell has a B.S. degree in Metallurgical Engineering from the University of Illinois and a M.S. degree from the University of Florida in Materials and Science and Engineering.
He began his career in 1986 at the Naval Aviation Depot in Pensacola, Florida. In 1989 he joined NASA’s Kennedy Space Center supporting the Shuttle Engineering Project Office serving as a Materials and Processes (M&P) Engineering expert. In 1996, Russell left NASA and worked in aircraft manufacturing and design at The Aerostructures Corporation in Nashville, Tennessee, and Bell Helicopter in Ft. Worth, Texas. In 2001, he rejoined the Shuttle Program working for the United Space Alliance at Kennedy Space Center.
In 2004, Russell rejoined NASA serving as the Aging Aircraft Principal Engineer for the Orbiter Project Support Office. In 2009, he became a member of the Materials Science Division at the Kennedy Space Center supporting the Orion Multi-Purpose Crew Vehicle and assisting in the development of requirements for the Commercial Crew Program. In 2012, Russell was named the Chief of the Materials and Processes Engineering Branch. In 2014, he joined the Commercial Crew Program as both the spacecraft and launch vehicle Systems Manager for Specialty Engineering (Materials and Processes and Fracture Control).
Light Metals Division Lecture
Speaker: Mark Easton, RMIT University
Lecture Title: "Near Net Manufacturing of Light Metal Alloys"
Date: Tuesday, March 16
Time: Noon EDT
About the Presentation
Near net shape manufacturing of a component shape and appropriate properties for its function can be achieved in one processing step. Benefits can include processing and material efficiency resulting in low cost and a potentially lower environmental impact. Light Metals have been commonly used in near net shape manufacture. Aluminium castings are almost ubiquitous in automotive applications as gravity, permanent mould, and high pressure die castings. Magnesium alloys can enable further design freedom, with thinner walled and more complex castings enabling part consolidation and great functionality. More recently, additive manufacturing has taken net shape processing to another level with highly complex structures, with graded properties enabling applications in biomedical, aerospace, and other industries that were unthought of just a few years ago. Whilst there appears to be a big difference between an automotive wheel casting and an orthopedic lattice structure implanted in a hip joint, the manufacturing challenges are similar: control of microstructure, accommodating solidification shrinkage and defect formation, optimization of properties, and design innovation through increasing part complexity. This talk will highlight the development of near net shape manufacturing of light metal alloys.
About the Speaker
Mark Easton is currently the Associate Dean (Manufacturing, Materials and Mechatronics) at RMIT University, where he has been since 2014. Prior to this, he was at Monash University, where he primarily worked with the CAST Co-operative Research Centre and was its final CEO. Easton’s Ph.D. is from the University of Queensland, and he has also had stints at Comalco (now Rio Tinto Aluminum) Research Centre and at the Leichtmetallkompetenz Zentrum, Rashofen (LKR) in Austria. He is the winner of a number of awards including the Henry Marion Howe Award and the GKSS Magnesium Award. Whilst at the CAST CRC, he received five commercialization awards for his role in the commercialization of technologies. He has more than 20 years of experience in solidification processing of light alloys, initially focusing on casting, but he has more recently joined the additive manufacturing bandwagon.
Award Lectures
Extraction & Processing Division Distinguished Lecturer
Speaker: Rodney Jones, Mintek
Lecture Title: "Ferronickel - Thermodynamics, Chemistry, and Economics"
Date: Monday, March 15
Time: 8:40 a.m. EDT
About the Presentation
Ferronickel is used for producing stainless steel and other ferrous alloys. Therefore, the smelting of nickel lateritic ore to produce ferronickel is of great importance to the stainless steel industry. A novel simple thermodynamic model allows one to map the relationships between the Fe:Ni ratio in the ore and the FeNi grade and Ni recovery. The chemical composition of the lateritic feed material, especially the SiO2/MgO ratio, strongly affects the composition of the slag, and how the furnace is operated. The choice of the FeNi product grade is affected primarily by economic and marketing considerations. A blend of thermodynamics, chemistry, furnace design and behavior, and economics allows good choices to be made around a particular project. The talk will also touch on a little of the history of laterite smelting and will provide a brief overview of world FeNi production.
About the Speaker
Rodney Jones is a chemical engineer and metallurgist with over 35 years of pyrometallurgical experience in a wide variety of processes that have been taken from concept to industrial implementation. He worked as a Senior Technical Specialist in the Pyrometallurgy Division at Mintek. He holds a BSc(Eng) degree in chemical engineering from the University of the Witwatersrand (Wits) in Johannesburg, a BA degree in logic and philosophy from the University of South Africa, and MSc(Eng) and PhD degrees in metallurgical engineering from Wits University. He is a registered Professional Engineer, a Past President and Honorary Life Fellow of the Southern African Institute of Mining and Metallurgy (SAIMM), and a Fellow of the Institution of Chemical Engineers (IChemE), the South African Institute of Chemical Engineers (SAIChE), and the South African Academy of Engineering (SAAE). He is an Honorary Adjunct Professor in the School of Chemical and Metallurgical Engineering at the University of the Witwatersrand and has previously held visiting positions in the USA and Australia. He is the author of Pyrosim software, used in 22 countries around the world, for the steady-state simulation of pyrometallurgical processes. Jones has also been part of the team that developed processes for the large-scale industrial application of direct-current arc furnace technology to the smelting of chromite in South Africa and Kazakhstan, ilmenite smelting in South Africa, cobalt recovery from slags in Zambia, battery recycling in Switzerland, ferronickel production in New Caledonia, and recovery of platinum from chromium-containing ores and wastes. The South African National Research Foundation rated him in 2009 and 2015 as an 'Internationally Acclaimed Researcher'. Jones is also a member of the Board of Trustees for OneMine.org and serves as the Chairman of the International Committee on Ferro-Alloys (ICFA).
William Hume-Rothery Award
Speaker: Ji-Cheng (JC) Zhao, University of Maryland
Lecture Title: "High-Throughput Measurements of Composition-Dependent Properties of Alloy Phases for Accelerated Alloy Design Presentation"
Date: Monday, March 15
Time: 8:35 a.m. EDT
About the Presentation
This talk will highlight recent advances in high-throughput measurements of alloy phase diagrams and phase-based properties. Diffusion multiples offer an efficient means to determine alloy phase diagrams via local equilibrium analysis at phase interfaces. Micron-resolution property measurements on composition gradients created in diffusion multiples allow effective collection of composition-dependent properties such as conductivity and elastic constants. A forward-simulation analysis allows accurate measurement of both impurity (dilute) diffusion and interdiffusion coefficients for the establishment of reliable diffusion (mobility) databases. Dual-anneal diffusion multiples (DADMs) allow rapid collection of large and systematic datasets on phase precipitation kinetics and morphological evolution across wide ranges of compositions as a function of time and temperature. Such datasets will be very valuable to testing and improving models. Examples will be used to illustrate the effectiveness and future essentiality of tight integration of computational and experimental approaches to rapidly establish digital materials property databases for accelerated alloy design.
About the Speaker
Ji-Cheng (JC) Zhao joined the University of Maryland in July 2019 as Minta Martin Professor and Chair of the Department of Materials Science and Engineering (MSE). He was a professor at The Ohio State University (OSU) from 2008 to 2019, during which he took a leave from OSU from 2014 to 2017 to serve as a Program Director at the Advanced Research Projects Agency-Energy (ARPA-E). Before joining OSU, Zhao was a materials scientist at GE Global Research for 12 years (1995–2007). His research focuses on determination of phase diagrams and various materials properties, computational thermodynamics, and design of advanced alloys. Zhao holds 48 U.S. patents and was the 2001 winner of the prestigious Hull Award from GE. An alloy he co-invented is widely used in GE gas turbines. The invention of ultrafast laser materials property microscopy by the Zhao-Cahill team was a finalist of the 2018 Berthold Leibinger Innovationspreis. He serves on the ASM Board of Trustees for the 2019—2021 term. Zhao was selected to receive the 2021 TMS William Hume-Rothery Award “for development of groundbreaking methodologies for systematic measurements of phase-based properties for the understanding of a very large number of alloy systems.”
Institute of Metals/Robert Franklin Mehl Award
Speaker: Tresa Pollock, University of California, Santa Barbara
Lecture Title: "New Superalloys in the Co-Ni Design Space"
Date: Tuesday, March 16
Time: Noon EDT
About the Presentation
The recently recognized existence of the ternary L12 intermetallic Co3(Al,W), not observed in the constituent Co-Al, Al-W or Co-W binaries, has opened up opportunities for design of a new class of high-temperature superalloys. Advances in Ni-base superalloys, which have been the subject of decades of alloy development, have been synonymous with advances in the performance and efficiency in aircraft and power-generation turbines, rocket engines, fuel cells and nuclear power plants. Given that Ni-base superalloys are chemically complex, often containing 6 – 10 “major” alloying elements along with 3 – 5 “minor” elements, similar chemical complexity is expected for cobalt alloys. The role of new experimental, computational and data-centric design tools in discovering new alloys in this domain will be discussed. Ni additions to these new Co-base alloys are useful for tuning transformations, enabling these materials to be produced along cast, wrought, and additive manufacturing paths. The unique properties of Co-Ni alloys will be discussed, along with future challenges for the exploration of the Co-Ni design space.
About the Speaker
Tresa Pollock is the Alcoa Professor of Materials at the University of California, Santa Barbara. Her research focuses on the mechanical and environmental performance of materials in extreme environments, unique high temperature materials processing paths, ultrafast laser-material interactions, alloy design, and 3-D materials characterization. More specifically, Pollock’s recent projects include the development of new femtosecond laser-aided 3-D tomography techniques and damage detection and modeling by resonant ultrasound spectroscopy. Prior to this work, she was employed at General Electric Aircraft Engines, where she conducted research and development on high temperature alloys for aircraft turbine engines and co-developed the single crystal alloy René N6 (now in service). Pollock also served as a professor in the Departments of Materials Science and Engineering at Carnegie Mellon University and the University of Michigan. She has been elected to the U.S. National Academy of Engineering and is a Vennevar Bush Fellow and Fellow of TMS and ASM International. Pollock is currently the editor-in-chief of the Metallurgical and Materials Transactions family of journals and was the 2005 TMS President. She earned her B.S. in metallurgical engineering from Purdue University in West Lafayette, Indiana, and her Ph.D. in materials science and engineering from the Massachusetts Institute of Technology in Cambridge, Massachusetts.
Symposium Keynotes
Magnesium Technology 2021 Symposium Keynote Speaker
Speaker: Warren Poole, The University of British Columbia, Canada
Lecture Title: "Measurement of the Critical Resolved Shear Stress for Slip in Mg Alloys Using Instrumented Indentation"
Date: Monday, March 15
Time: 8:30 a.m. EDT
About the Presentation
A critical challenge for the plasticity and fracture of magnesium and its alloys is the competition between the different deformation modes and how this changes with temperature. In the current study, the critically resolved shear stress for basal slip as a function of alloy composition and temperature has been measured using instrumented spherical indentation. Indentation offers the advantage that tests can be conducted on grains of known orientation in polycrystal samples, particularly of importance for alloys where producing single crystals is difficult. Here, it will be demonstrated that by doing tests with indenters of different radii, the critically resolved shear stress (CRSS) can be extracted. Very good agreement was found between the CRSS values for basal slip by indentation and the literature values from single crystal tests. Finally, the contribution will also offer perspectives on quantifying additional deformation modes such as extension twining and 2nd order pyramidal slip.
About the Speaker
Warren Poole is Professor in the Department of Materials Engineering at The University of British Columbia and holds the Canada Research Chair in Through Process Modelling of Advanced Structural Materials and the Rio Tinto Aluminium Chair in Materials Process Engineering. He obtained his Ph.D. at McMaster University, which was followed by an NSERC Post Doctoral Fellowship at the University of Cambridge, UK. Poole has published over 200 journal and conference papers related to the deformation, fracture, and microstructure evolution in light alloys and steels. He has given over 75 invited talks and is the recipient of the 2017 Acta Materialia Holloman Award, the Dean’s Medal of Distinction (2017), 16 best paper/poster awards, the 2013 Canadian Metal Physics Award, the 2014 Award of Excellence from the International Magnesium Association, a Killam Research Fellowship, and the Alan Blizzard Award for excellence in teaching.
Young Professional Award Lectures
Young Innovator in the Materials Science of Additive Manufacturing Award Lecture
Speaker: Michael Kirka, Oak Ridge National Laboratory
Lecture Title: "Additive Manufacturing of High-Temperature Metals: Present and Future Opportunities"
Date: Tuesday, March 16
Time: 11:00 a.m. EDT
About the Presentation
Technical advancements of the prior century in the manufacture and performance of high-temperature metals have been driven by scientific progress in the areas of casting, powder processing, and alloy design. The emergence and maturation of additive manufacturing technologies has opened a plethora of new processing routes for high-temperature materials and has begun to enable previously unlockable materials innovations and design opportunities. Additive manufacturing technologies such as electron beam powder bed fusion can be considered to reside at the intersection of the traditional fields of welding, powder metallurgy, and casting. Prior knowledge established from these parent fields is instrumental in the development of additive processing; however, additive is at the same time distinctly different due to the complex nature of the thermomechanical process history. Recent efforts in electron beam processing have enabled successful printing of difficult-to-process systems such as nickel-based superalloys and has opened new opportunities for exploration of refractory systems. Looking forward, additive will make possible the fabrication of components with engineered hierarchical microstructures tailored for in-service optimized performance.
About the Speaker
Michael Kirka is the Group Leader of the Deposition Science and Technology Group at Oak Ridge National Laboratory (ORNL). His current research focuses on developing and understanding the limitations in the processing science for high-temperature materials such as nickel-base (Ni-base) superalloys and refractory metals for additive manufacturing processes through understanding their microstructural evolution and resultant process-structure-property relationships. Additionally, Kirka’s work has focused on understanding the long-term mechanical behavior and degradation mechanisms in additive manufacturing materials similar to those observed during service. He joined ORNL in 2014 as a post-doctoral fellow. Kirka earned his B.S. in materials science in 2007 from The University of Michigan, and M.S. and Ph.D. degrees from The Georgia Institute of Technology in mechanical engineering in 2010 and 2014.
Young Professional Tutorial Lecture
Date: Tuesday, March 16
Time: Noon to 1:05 p.m. EDT
Speaker: Wei Xiong, University of Pittsburgh
Lecture Title: "Integrated Computational Materials Design for Alloy Additive Manufacturing"
About the Presentation
Additive manufacturing, as a versatile technique, can produce complex shape components directly for engineering applications. However, it is challenging to perform a comprehensive design for additive manufacturing processes due to its unique microstructure attributes generated by the complex melting/sintering process. The Integrated Computational Materials Design method can be applied to accelerate the new alloy development and processing optimization in additive manufacturing. The method integrates multiscale microstructure engineering approaches, and especially uses the CALPHAD-based ICME approach as a guide tool, to reveal the process-structure-property relationships. Through the development of the CALPHAD-based ICME methods in the Physical Metallurgy and Materials Design Laboratory at the University of Pittsburgh, we are designing different types of high-performance alloys for additive manufacturing and further improving the post-processing of as-built components, which are manufactured by powder-bed fusion and directed energy deposition. In turn, additive manufacturing has also been used as a tool for rapid prototyping to assist in new alloy discovery.
This presentation will be of interest to researchers, engineers, and students who are interested in phase transformations, new alloy development, additive manufacturing, and ICME.
Wei Xiong is the director of the Physical Metallurgy and Materials Design Laboratory at the University of Pittsburgh. He is an assistant professor in the materials science program since September 2016. Xiong got his Ph.D. degree (focus: computational thermodynamics and physical metallurgy) from KTH Royal Institute of Technology and Doctor of Engineering degree (focus: powder metallurgy) from Central South University. In 2012, he moved from Sweden to the USA after his Ph.D. research program. He stayed one year at the University of Wisconsin – Madison before joining Northwestern University as a research associate for alloy development from 2013 to 2016. Using CALPHAD-based ICME tools and advanced manufacturing techniques, he works in materials design based on process-structure-property relationships. Xiong serves on the TMS Alloy Phases Committee (vice-chair), TMS High-Temperature Alloys Committee, TMS Additive Manufacturing Committee, and ASM International Alloy Phase Diagrams Committee. He has received several academic awards, which include: Best Paper Awards of the CALPHAD journal in 2012 and 2013, and the TMS Functional Materials Division Young Leader Professional Development Award 2015. Xiong serves as an associate editor of the journal Science and Technology of Advanced Materials, and an editorial advisory board member of the journal Materials Characterization.
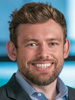
Speaker: James Pikul, University of Pennsylvania
Lecture Title: "Electrochemical Healing of Metals: A New Way to Repair Additive and Cellular Metals at Room Temperature"
About the Presentation
Structural materials in biology can heal fractures at room temperature, whereas metals require elevated temperatures and large energy inputs. As a consequence, modern engineering design follows an approach where a part is optimized to withstand all future loading cases in the part’s projected lifetime. This approach has been highly effective, but results in concepts like safety factors, which increase the weight and volume of the part beyond what's necessary in normal loading conditions. Biology presents compelling alternatives, such as in bone, where ‘parts’ are efficiently produced to withstand most loading cases and, when an extreme case is encountered, the bone can be repaired without being replaced. Manmade structural materials that could heal like bone would have several advantages. A major challenge, however, has been realizing structural metals that can be effectively healed without an expert (in the case of welding, which is prohibitive in complex additive parts) and without high temperatures which consume lots of energy and degrade nearby materials. Recently, we have demonstrated a new rapid, effective, low-energy, and room-temperature approach for healing cellular metals using electrochemistry and polymer-coated cellular metals, which mimic the transport-mediated healing of bone.
In this presentation, I will discuss the advantages of electrochemical healing of metals, new design strategies that emerge through the combined optimization of mechanics and electrochemical transport, and how this approach enables the repair of complex metal parts realized from 3-D printing whose internal geometry prevents repair using current technologies. The combination of electrochemistry, mechanics, transport limited processes, and 3-D structured metals will interest TMS members across diverse areas, such as additive technologies, materials processing, mechanics, corrosion, light metals, and materials design.
About the Speaker