|
Date: | Monday, March 4, 2013 |
Location: | Lila Cockrell Theater, San Antonio Convention Center |
Chaired by: | Les Edwards, Rain CII Carbon |
The rapid growth in aluminum production over the last ten years has placed additional demands on the raw material supply chain including bauxite, alumina, petroleum coke and coal tar pitch. Rising impurity levels in petroleum coke, for example, are causing smelters and aluminum end users to look more closely at impurity level specifications. This keynote session will include invited presentations from leading industry experts that examine the role and outlook for impurities across the aluminum supply chain.
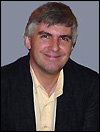 |
STEPHEN LINDSAY
Alcoa Inc.
Topic: "Raw Material Impurities and the Challenge Ahead"
The impurities contained in the raw materials that are used by the aluminum industry pose challenges that must be managed from various perspectives. These include: product qualities, costs, and impact upon the work environment and that of the surrounding area. As the industry continues to change, changes in impurities will take on greater meaning for process control, metal products, and environmental, health and safety. The author provides his insights to these emerging issues.
|
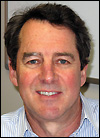 |
JAMES METSON
University of Auckland
Topic: "Impacts of Impurities Introduced into the Aluminium Reduction Cell"
Impurities enter the aluminium reduction process through raw materials and operational practices. The declining quality of petroleum cokes, and the steadily increasing efficiency in the capture and recycle of pot fumes, increase impurities, impacting both cell performance and metal quality. Aluminas are also a key and variable impurity source, with little incentive for producers to drive purity improvements. Beyond metal quality, the critical impacts lie in pot operations where control, or even analysis, of bath chemistry becomes increasingly problematic. Impurities have measureable impacts on current efficiency, and on anode effects, driven by inability to efficiently dissolve alumina. Impurity reduction strategies have been driven by perceived problem elements, for example phosphorus; however, these processes generally entail an unacceptable level of collateral alumina loss. It may well be time to revisit the potential to lower impurity inputs, for example in alumina and in operations, and to look again at potential stripping techniques.
|
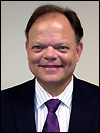 |
KARL BARTHOLOMEW
KBC Advanced Technologies, Inc.
Topic: "Changes in Global Oil Refining and Its Impact on Anode Quality Petroleum Coke"
The global refining industry has undergone a dramatic upheaval over the past decade. From the mid-2000s when a "Golden Age" was underway, through two years of losses and concerns about ‘peak oil,’ to today’s unique crude supply situation in the mid-Continent United States, refiners have never been more challenged in their feedstock supply strategy. This presentation will review the main economic drivers for refining, including the impact on petroleum coke production. How the markets (and decisions) have changed over the past decade will be examined, and scenarios of what’s ahead will be covered. Arguably the biggest change affecting the U.S. downstream energy market is the rapid development of shale oil supply. Shale oil production, along with changes in global refining capacity (and coking capacity) – additions and closures – could soon have profound implications for the quality and quantity of calcinable anode grade petroleum coke.
|
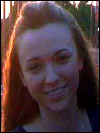 |
ANDREA WEBER
Rio Tinto – Sebree Works
Topic: "Impact of Higher Vanadium Levels on Smelter Operations"
In early 2011, the RTA Sebree smelter experienced a significant increase (~100ppm) in calcined coke vanadium levels to levels around 410-440ppm. This was driven by crude oil changes at a refinery supplying one of the primary cokes used in the coke blend supplied to the smelter. The paper discusses the impact of the change on carbon consumption and some of the actions taken by the smelter to respond to the change. Data is presented showing the impact on process metrics such as anode consumption, unscheduled anode changes, current efficiency, power consumption and primary metal quality. The presentation will show that changes of this magnitude can be managed with an appropriate understanding of key performance drivers and a focused technical improvement plan.
|
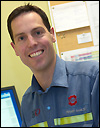 |
STEWART HAMILTON
New Zealand Aluminium Smelters
Topic: "Impact on Smelter Operations of Operating High Purity Reduction Cells"
Over the last 15 years New Zealand Aluminium Smelters Limited (NZAS) has developed and implemented technology and operating practices to produce High Purity (Al 99.90+) and ultra High Purity (Al 99.97+) ingot. In the challenging macro-economic climate of falling LME, weakening exchange rates, and increasing power prices, the High Purity strategy has enabled NZAS to maximize value and maintain global leadership in High Purity smelter grade aluminium production. The NZAS journey to High Purity production and the impact that this strategy has had on the complexity of smelter operations are outlined. The operational focus necessary to successfully implement the High Purity strategy is also required to improve all facets of smelter operations. Data will be presented to show the impact recent challenges, such as reducing quality of raw materials, are having on Smelter operation and how these are being managed to maintain High and Ultra High purity production economically.
|
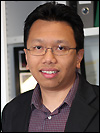 |
MUHAMMAD AKBAR RHAMDHANI
Swinburne University of Technology
Topic: "Management of Impurities in the Aluminium Cast House"
The concentration of impurities in raw materials (particularly petroleum coke) is increasing and testing the ability of cast houses to meet customer chemical specifications. Much of the metal content (Ni, V) of the coke and impurities in alumina (Fe, Si, Ga, Zn) reports to the aluminium in the reduction cells. These impurities can have detrimental effects in certain alloys. This presentation will review options for removing impurities in the cast shop. Classical melt treatment processes of salt fluxing, degassing and filtration used to remove alkali metals and solid particles are reviewed. Aluminium boride treatment can be used to remove titanium, chromium, and vanadium. Current work on the mechanisms of this process is examined. An investigation into potential for a melt nickel removal process is recapped. Past work on iron removal is reviewed and those processes used for producing super purity aluminium are also listed and discussed.
|
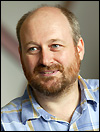 |
JOHN GRANDFIELD
Grandfield Technology
Topic: "An Initial Assessment of the Effects of Increased Ni and V Content in AA6063 and A356 Alloys"
Changes in calcined coke composition associated with different crude oil sources have caused nickel and vanadium levels in aluminum to rise. To ensure cast product quality is not compromised, an understanding of the effects of these changes is needed. An initial investigation has been conducted for two commonly used alloys, AA6060/6063 and A356. Castings were produced with low typical levels of NiV and with high NiV levels approaching the maximum P1020 specification of 300ppm each. Microstructural changes were assessed using optical and scanning electron microscopy, and tensile properties and corrosion resistance were measured. For AA6060/6063 alloy, there was no significant difference in the tensile properties of extrusions with low and high NiV levels, but a small drop in corrosion performance was measured at high NiV levels. For as-cast A356 alloy, there was no significant difference in corrosion performance, but adding Ni and V had a small effect on tensile properties.
|
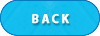
|