|
Date: | Monday, February 17, 2014 |
Organized by: | Barry Sadler, Net Carbon Consulting |
Over several decades, research and development within the Aluminum industry has been constrained by factors
such as cost cutting and "rationalisation" following Company mergers and take-overs. This leads to a question - "How will the industry support the work required to move on to the next innovation S curve?", e.g. how to get to the critical mass of R&D required to achieve the breakthroughs that can lift industry environmental and energy efficiency performance to that required to maximise future growth potential? Relevant to this are issues such as: What work is needed? Who will do it? What are the possible funding models? What are the roles for international cooperation and government facilitation?
In this plenary session, senior speakers from Industry and Academia will explore these topics from the perspective of Smelting and Alumina production,
look at the role of external research providers, present a case study from one integrated Aluminium company, look at innovation in the industry from a
North American perspective, and for comparison, examine innovation within the broader mining industry. The presentations will be followed by a panel
discussion.
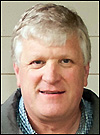 |
DR. BARRY SADLER
Managing Director, Net Carbon Consulting Pty Ltd
Topic: Opening Comments
Time: 8:30 – 8:35am
|
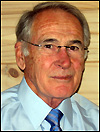 |
EMERITUS PROF. BARRY WELCH
Universities of New South Wales (Australia) & Auckland (New Zealand), Director Welbank Consulting Ltd.
Topic: "Focus areas and possible options for aluminium smelter performance enhancement"
Time: 8:35 – 9:20am
This provocative presentation will highlight how the emphasis on good smelting technology fundamentals of has declined, yet numerous opportunities exist for economic and performance enhancements. Speculative examples will be promoted for addressing the energy and operating inefficiencies that persist in smelting. After 80 years of research, there is no alternative process for aluminium production other than electrowinning with a carbon anode in a molten fluoride electrolyte, so this is where this presentation will be focused.
Over the last 60 years or so, the aluminium smelting industry has moved from largely fully vertically integrated companies (i.e. bauxite mining to semi-finished products) to the much more stand-alone industry we have today. Due to a number of diverse factors, such as the dependency of independent smelters on purchased technology, this has diminished the "pool" for developing innovative ideas. Progress in technology development became retarded by a "copy and paste" syndrome. This has led to an inward thinking industry that has not looked "over-the-fence" to the advances made in other industries that have the potential for application in large modern smelters.
The scientific understanding of smelting principles has reached such a low that the industry does not even correctly define what an anode effect is. While computer modelling is widely used to refine cell designs, it has significant limitations such as the use of simplified background equations that are based on data developed for quite different electrolytes, cell designs and operating conditions to those now used. Little attempt has made to the bridge the gap between business units especially since short term financial performance carries higher rewards for management as compared with longer-term, process wide improvements. But needs and solutions are there if the industry opens its eyes and appreciates the long-term benefits of further research and development.
|
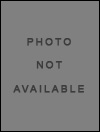 |
DR. GERALD I.D. ROACH
Technical Manager, Extraction Technology, Alcoa World Alumina, Kiwana, Western Australia
Topic: "Further innovation in the Bayer process – is this a reality or a pipe dream?"
Time: 09:20 – 10:05am
Over the last century the rapid growth in aluminium demand has seen the Bayer process, used to produce smelter-grade-alumina, increase in both output and efficiency. Innovation within the Bayer process related to equipment (e.g. fluidised bed calciners), yield, solid/liquor separation techniques, energy reduction, as well as making the process essentially a continuous operation, has resulted in a major reduction in operating costs and often (but not always) capital cost. There have been similar major improvements in Safety and the Environmental footprint. With such a mature process the expectation might well be that the top of the S curve has been reached in many of the various unit operations, and the overall process, such that there is not much more room for improvement or innovation.
The presentation will review improvements within the Bayer Industry and look at whether there is potential for really significant innovation to move the Bayer Process on to a new S curve. In particular, a major factor in the cost of alumina production (both capital and operating cost) is the smelting processes’ product quality requirements.
In order to move forward and identify, and then develop, new innovations it is important that these innovations can be shown to be implementable processes. That requires significant process input and continual close cooperation between Industry and Academia or the relevant Research organisation (even between the Refinery and their own Research Group) to ensure the project does not stray from its’ primary goal. It is important to develop a model for such cooperative work to ensure that there is a win/win scenario for all parties as often views of what constitutes a successful project, and expectations from the project, can be markedly different.
|
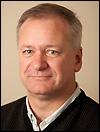 |
PROF. MARK P. TAYLOR
Chemical and Materials Engineering Dept., Director, NZ Product Accelerator, University of Auckland
Topic: "The role of external research groups in Aluminium Industry innovation"
Time: 10:05 – 10:40am
This presentation will look at the role of external research groups in undertaking and fostering innovation within the Aluminium
Industry. It will drill down into the process of innovation in industry, and look at some specific examples where external
research groups have contributed to successful innovation.
|
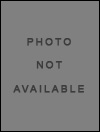 |
DR. MARTIN SEGATZ
Manager Strategic Technology Program, Hydro Aluminium Deutschland GmbH
Topic: "Hydro's Innovation Engine - From Idea to Business"
Time: 10:50 – 11:15am
This presentation will look at how Hydro's aspiration to become technology leader in key areas of its vertically integrated
aluminium business has been the driving force to establish a durable network of intense cooperative research relationships
with preferred academic and industrial partners. A focus on business-critical development needs like energy efficiency in
Primary Metal or new product development opportunities in the Rolled Product sector, have allowed Hydro to maximise the effect
of its R&D efforts, creating business value and opportunities. A systematic approach to innovation management and well defined
internal development processes have resulted in major technology and business achievements. By professionally managing contracts
and IP, Hydro has been able to cooperate successfully and efficiently with research and funding partners even in key areas of
core technology and thus extend its own capabilities significantly. The potential for the wider application of Hydro’s approach
within the industry will also be discussed.
|
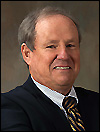 |
DR. ALTON TABEREAUX
Alcoa (retired), Consultant, USA
Topic: "Innovation in the North American aluminum industry"
Time: 11:15am – 11:40am
In 2013 Alcoa’s celebrated its 125 year anniversary of the company start by its innovative legacy of founders Charles Martin
Hall and Alfred Hunt. This presentation will look at the innovations and evolution of aluminum smelting technology in North
America since that creation with an emphasis of the impact of corporate and government R&D programs on the process. Specific
examples of R&D work within the North American aluminum smelting industry will be looked at, including the inert anode,
carbothermic reduction, new metal product development, and large scale cell development. |
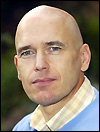 |
GEOFF BEARNE
General Manager Innovation, Rio Tinto
Topic: "Innovation in Mining – Rio Tinto’s Mine of the Future™ programme"
Time: 11:40am – 12:10pm
The mining industry faces growing challenges to meet the increasing demand for metals and minerals, driven largely by
industrialisation and urbanisation in the emerging world. Today, quality mineral deposits are harder to find, are often
remotely located and tend to be of lower ore grade. Step change innovation is required to maintain competitive advantage
in the face of rising costs and declining productivity. Rio Tinto’s Mine of the FutureTM programme aims to create value by
finding better ways to mine through new technologies. Challenges for the mining industry and Rio Tinto’s innovation initiatives
are discussed, while reflecting upon some experiences in the aluminium industry.
|
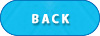
|