Live Event Dates: September 28, October 1, 6 and 8, 2020
Superalloys are materials designed for high-temperature applications where strength and corrosion resistance are essential traits. Since their popularization in the mid-twentieth century, superalloys continue to be developed with specific applications in mind for use around the world. These webinars will show the latest developments from research conducted in universities, government laboratories, and industry, from studies on alloy properties, new processing techniques, and even repairing damaged superalloys.
Registration
|
Cost |
Member |
Free |
Nonmember |
$100 |
Session 1 - Monday, September 28, 2020, 11 am to 12:30 pm EDT
Moderator
Jonathan Cormier, ENSMA - Institut Pprime - UPR CNRS 3346
Presenters
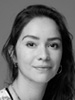
Marie Charpagne and Jean-Charles Stinville, University of California, Santa Barbara
"Fatigue Deformation and Plastic Localization in Polycrystalline Nickel-based Superalloys"
Critical mechanical properties of nickel-based superalloys components are controlled by plastic deformation that develops during service at the scale of the microstructure. During cyclic loading, the localization and accumulation of plasticity at specific microstructure features leads to damage nucleation and ultimately rupture of the part. The microstructural configurations that favor early plastic localization and fatigue crack nucleation in polycrystalline nickel-based superalloys are highly dependent of the loading conditions (fatigue regime, temperature and environment). In advanced polycrystalline nickel-based superalloys, competing failure modes (oxidation-assisted initiation, inclusions and annealing twin initiation) are observed, along with an inversion of the temperature dependence of fatigue strength from the low to high cycle fatigue regime. These phenomena can be directly linked to the intensity of the plastic localization that occurs at the scale of the physical mechanisms of dislocation slip. The investigation of the plastic localization at the sub-grain scale for different polycrystalline nickel-based superalloys shows a close relation between fatigue strength of the alloys and intensity of the slip localization. From this observation, a novel approach that consists of minimizing plastic localization at the sub-grain scale by adjusting the microstructure of the alloys is pursued.
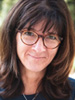
Nathalie Bozzolo, MINES-ParisTech
"Recrystallization Phenomena in Nickel-based Superalloy Forgings"
The most usual phenomenon controlling the final grain size while forging nickel-based superalloys is known to be dynamic recrystallization proceeding discontinuously through necklace nucleation. Post-dynamic evolutions may nevertheless also be of utmost importance in the control of the final microstructure in a large forging after cooling down to room temperature. Apart from this usual behavior, more exotic phenomena can also take place under specific thermomechanical conditions, among which:
- critical static recrystallization leading to the overgrowth of few grains,
- or heteroepitaxial recrystallization of 𝛾 grains on 𝛾’ primary precipitates,
- or the formation of 𝛾’ precipitates close to a twin relationship with the matrix grain as a result of the interaction between a recrystallization front with preexisting precipitates.
Both the experimental analysis of these phenomena and their simulation will be addressed in the talk.
Session 2 - Thursday, October 1, 2020, 8 am to 9:20 am EDT
Moderator
Akane Suzuki, GE Research
Presenters
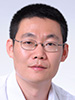
Jian Zhang, Institute of Metal Research, Chinese Academy of Sciences, Shenyang, China
"Directional Solidification of Superalloys: Processing, Microstructure and Mechanical Properties"
Directional solidification has been widely used in industry to produce DS and SX superalloy components nowadays. Two directional solidification processes, high rate solidification (HRS) and liquid metal cooling (LMC), and the corresponding microstructure and mechanical properties are discussed in this presentation. Comparing to HRS, LMC provides higher temperature gradient, which leads to less defects, refined microstructure and improved properties of the single crystal. However, the process is also facing challenges, such as contamination from the metal coolant and large transverse thermal gradient. Formation mechanism of defects and their effect on mechanical properties as one of the key issues in both HRS and LMC processes has also been discussed in this talk. Typical microstructure features (PDAS, eutectic and micro-porosities) in SX alloys obtained by HRS and LMC has been compared. The role of micro-porosity during creep and fatigue was characterized in detail.
Kyoko Kawagishi, National Institute for Materials Science, Japan
"Development of Sixth-generation Single-crystal Superalloy TMS-238"
To improve the thermal efficiency of gas turbine engines, the composition of Ni-based single-crystal superalloys is constantly evolving in response to rising turbine inlet temperatures. Over the last decade, the addition of ruthenium (Ru) has been one of the main focus for increasing temperature capability and contributing to the development of new generation single crystal superalloys. In this presentation, the development of TMS-238, one of the latest Ru-containing sixth generation superalloys developed by the National Institute for Materials Science, will be reported. TMS-238 is a promising candidate alloy for future turbine blade applications due to its excellent and balanced mechanical and environmental properties.
Session 3 - Tuesday, October 6, 2020, 11 am to 12:30 pm EDT
Moderator
Sammy Tin, Illinois Institute of Technology
Presenters
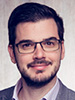
Paraskevas Kontis, Max-Planck-Institut für Eisenforschung GmbH
"Decoding the DNA of Superalloys for Future Alloy Design Strategies"
Every superalloy has a unique composition deriving from its individual DNA information, which is defined by alloy design constraints such as lattice misfit, density, γ’ volume fraction, cost and others. These genetic characteristics, i.e. alloy design constraints, are carefully selected for a given application aiming to achieve the required microstructure and mechanical performance. Recent studies have shown that the physical interactions of solutes with crystal defects at near atomic scale are an important genetic characteristic. Decoding these physical interactions can lead to improved alloy design strategies and more accurate life prediction models. In this webinar, new insights on such physical interactions in polycrystalline superalloys will be presented. Different types of crystal defects have been investigated in polycrystalline superalloys by electron microscopy and atom probe tomography. It will be shown that creep performance can be controlled by the different partitioning behaviour observed at different types of defects in γ’. In addition, partitioning of solutes at defects in intergranular borides will be presented, allowing to discuss a better understanding of their deformation and evolution during creep. Future challenges on decoding these physical interactions and how they can be exploited by our community will be discussed.
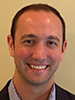
Tim Smith, NASA Glenn Research Center
"Enhancing the Creep Strength of Next-Generation Disk Superalloys via Local Phase Transformation Strengthening"
Co-authors: T.P. Gabb, NASA Glenn Research Center; K.N. Wertz, Air Force Research Laboratory; J. Stuckner, NASA Glenn Research Center; L.J. Evans, NASA Glenn Research Center, A.J. Egan, The Ohio State University, M.J. Mills, The Ohio State University.
A new disk superalloy has been developed by NASA to improve high temperature creep performance utilizing the recently discovered local phase transformation strengthening mechanism. Creep tests were performed at 760°C and 552MPa, to approximately 0.3% plastic strain, a regime where the formation of γʹ shearing modes such as superlattice extrinsic and intrinsic stacking faults are active. The new alloy exhibited superior creep performance over the current state-of-the-art superalloys, ME3 and LSHR. High resolution characterization confirmed the formation of the strengthening η phase along superlattice extrinsic stacking faults and χ phase along superlattice intrinsic stacking faults. In addition, creep deformation analysis via scanning transmission electron microscopy appears to show a significant reduction in microtwin formation as compared to LSHR and ME3. This improvement in creep performance was also accompanied by an improvement in both room temperature and high temperature strength.
Session 4 - Thursday, October 8, 2020, 8 am to 9:30 am EDT
Moderator
Mark Hardy, Rolls-Royce Plc
Presenters
Roger Reed and Tony Tang, Oxford/Oxmet
"Alloys-By-Design: Applications to New Superalloys for Additive Manufacturing"
New grades of γ/γ’ nickel-based superalloy are designed using computational approaches specifically for additive manufacturing. Account is taken to resist defect formation via solidification and solid-state cracking. Processing trials are carried out using powder-bed fusion laser fabrication, with the heritage alloys IN939 and CM247LC. Microstructural characterization, calorimetry and hot tensile testing are used to assess the approach employed. The new superalloys demonstrate superior synergy of manufacturability and mechanical properties. Suggestions are made for further optimizations to the modelling approach.
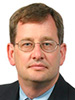
Eric Huron, GE Aviation
"Advancing The State of the Art of Superalloys by Balancing Performance with Repairability"
The expansion of commercial aviation has been enabled by advances in gas turbine technology. These advances have in turn been enabled by improvements in materials, including superalloys. The aviation propulsion community has developed new superalloy compositions and new processing methods, with the new alloys informally referred to as “generations” of superalloys. The early generation advances were focused primarily on high temperature mechanical properties such as creep, but it has become more critical to develop a “Life Cycle” understanding to extend operating lives and improve economics for superalloy components. Higher temperature strength and creep capability remain important but must be coupled with a more balanced development approach, with cyclic fatigue capability, environmental resistance, and repair methodology also critical to success. This presentation will discuss how interactive improvements in alloy composition, processing, environmental resistance, and repair technology are driving the aviation gas turbine industry forward and advancing the state of the art.